Technology
Abrasive Discs
Islands Prevent Hydroplaning
The flexible abrasive discs used for high speed lapping and polishing have an
annular band pattern of individual circular islands that are top coated with abrasive
particles. These islands prevent hydroplaning of the water-mist cooled wafers at
very high abrading speeds that can approach 100 mph (3000 RPM). Excess coolant
water is directed from the island tops to the recessed passageways between
adjacent islands. Wafer hydroplaning can cause the wafers to tilt which can cause
non-flat surfaces or cause the wafers to lift away entirely from the abrasive and stop
abrading altogether.
No Clean-Up Mess
Because the water mist coolant continually washes both the fixed-abrasive disc and
the wafer, the cleanup mess associated with conventional liquid abrasive slurry is
eliminated.
Disc Annular Islands
Wafers are positioned to slightly overhang both the inner and outer radii of the annual abrasive band. This is done to ensure that the abrasive on all the islands wears down uniformly without forming tracks. If tracks are formed in the abrasive, it will lead to uneven abrading patterns on subsequent workpieces processed with that same disc.
​
Abrasive Beads
Abrasive particle filled erodible beads are mixed with an industry-standard phenolic adhesive and coated on the top flat surfaces of the islands. These beads are filled with very small abrasive particles ranging from 45 microns to sub-micron sizes. During abrading, the erodible beads wear down, and a continuous supply of fresh and sharp abrasive particles become exposed. Because of the extremely large size of the beads (.015" dia.), they provide much longer abrading lives than more common small beads (.002" dia.). Abrasive materials can include diamond, aluminum oxide, CBN, or even silica (for final polishing of sapphire wafers).
Island Disc Backings
Each abrasive coated disc is made from a tough and heat resistant flexible polycarbonate backing substrate having integral island structures. The
substrate has a backing thickness of about .025” and the islands have a height of about .030”. The flexible disc has a continuous flat surfaced backing which allows it to be strongly attached to a rotating platen with vacuum. Less expensive polyester substrates can be used with E-Beam or UV cured phenolic adhesives.
Batch-Type Disc Production
Because of the necessity of having discs with annular bands of abrasive islands and continuous backing surfaces (for vacuum attachment of the discs to a platen), the abrasive discs are produced on a batch basis. This allows easy production of any type of disc as the backing can be produced without a specific abrasive particle type or size.
​
Island Disc Substrate Production
These disc substrates can be produced inexpensively by use of an extruder-die
supplying molten polycarbonate to a chill-roll drum having a pattern of island pocket
holes on its surface. The extruded island-web is solidified, and the disk substrates are
low-force die-cut from the heat-softened moving web. The remaining polycarbonate
web (weed) is then re-ground and fed back into the extruder. Disc substrate island top
surfaces can be cut on a lathe or ground flat prior to abrasive coating to provide
precision-flat islands and precision-thick discs.
Abrasive-Slurry Coated Discs
A uniformly thick coating of abrasive particles is mixed with a solvent-based phenolic
binder adhesive to form a liquid abrasive slurry. This slurry is coated on the
flat-surfaced island tops with the use of a precision thickness magnetic font sheet.
First,the font sheet is firmly attached to the island tops by a magnet positioned at the back side of the polycarbonate disc substrate. Port holes in the font sheet match the slightly larger island tops that support the font sheet. Next, these font holes are level-filled with the liquid abrasive slurry to provide a uniform thickness abrasive coating on each island. The slurry also assures that individual beads are uniformly distributed across the surface of the individual island tops. Finally, the disc is placed in an oven which evaporates the solvent in the adhesive and the cures the phenolic to secure the bead to the island top. Because the abrasive slurry is pre-mixed, each individual island has the same amount of abrasive material coated on it. Discs produced at different times have the same amount of abrasive and the same abrading performance.
Precision-Thickness Discs
The precision thickness of each disc varies by less than .0001” to assure full utilization of all the disc abrasive at high abrading speeds. Each disc is flattened after abrasive coating to provide an abrasive surface that is precisely flat and parallel to the backing surface. Because of the precision flatness of the platen, these index-marked discs can be used interchangeably and repetitively without reconditioning the abrasive flatness each time. These flexible and tough polycarbonate discs are quickly attached to the platen with vacuum. The typical hold-down vacuum force applied to a 12” diameter disc exceeds 1000 lbs.
Disc Diameters
Both 12” and 18” diameter abrasive island discs are used interchangeably on the prototype lapper machine. Larger 24” or 36” discs and machines can be produced for large 12” wafers (300mm).
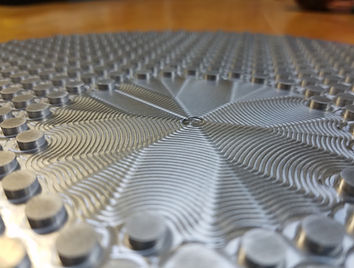

